Transparent PCB Substrate Manufacturer
Transparent PCB Substrate Manufacturer,Transparent PCB substrates are innovative printed circuit board materials designed to allow light transmission while providing electrical connectivity. Made from transparent materials like glass, acrylic, or polycarbonate, these substrates enable visibility of embedded components and traces. They find applications in decorative lighting, automotive displays, consumer electronics, and specialty industrial equipment, where both functionality and aesthetic appeal are crucial. With specialized manufacturing processes involving transparent conductive layers and careful design considerations, transparent PCB substrates offer a unique combination of practicality and visual elegance for various technological applications.
What is a Transparent PCB Substrate?
A Transparent PCB Substrate is a printed circuit board (PCB) material that allows light to pass through it, enabling visibility of components and traces embedded within. This type of substrate is often made from transparent materials like glass or certain types of plastics, such as acrylic or polycarbonate.
Transparent PCBs are primarily used in applications where visual inspection or aesthetic appeal is important, such as in decorative lighting, automotive displays, consumer electronics, and specialty industrial equipment. They offer advantages like enhanced design aesthetics, easy identification of components, and the ability to integrate lighting elements directly into the PCB itself.
In terms of manufacturing, producing transparent PCBs involves specialized processes to ensure the substrate maintains its transparency while still providing the necessary electrical and mechanical properties required for reliable operation. This might include using transparent conductive materials for traces and pads, as well as carefully controlling the thickness and composition of the substrate material.
Overall, Transparent PCB Substrates offer a unique combination of functionality and visual appeal, making them a preferred choice for various applications where both practicality and aesthetics are important.
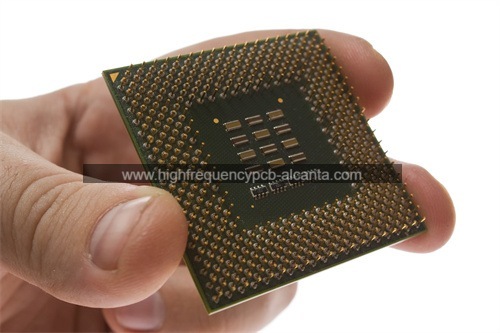
Transparent PCB Substrate Manufacturer
What are Transparent PCB Substrate Design Guidelines?
Designing with transparent PCB substrates requires careful consideration to ensure optimal performance and visibility. Here are some general design guidelines:
- Material Selection: Choose a transparent substrate material suitable for your application. Common options include glass, acrylic, or polycarbonate. Consider factors such as thermal stability, mechanical strength, and compatibility with your manufacturing processes.
- Layer Stackup: Design an appropriate layer stackup considering the transparency requirements and the electrical performance of the PCB. Keep in mind that additional layers or opaque materials may affect transparency.
- Trace Design: Use transparent conductive materials for traces and pads to maintain visibility. Indium tin oxide (ITO) is commonly used for transparent conductive layers due to its high transparency and conductivity.
- Component Placement: Place components strategically to minimize obstruction of light transmission. Avoid placing opaque components directly in the path of light if transparency is a priority.
- Clearance and Spacing: Maintain adequate clearance and spacing between traces, components, and layers to prevent light obstruction and ensure electrical reliability.
- Lighting Integration: If the PCB is intended to be used for lighting applications, design for integration of lighting elements such as LEDs directly into the substrate. This may involve incorporating light-guiding structures or diffusers into the PCB design.
- Surface Finish: Choose a surface finish that enhances transparency and provides protection against environmental factors. Options may include clear coatings or finishes that improve scratch resistance without compromising transparency.
- Thermal Management: Consider thermal management strategies to dissipate heat generated by components, especially if the PCB is enclosed or operates in environments with temperature variations. Transparent substrates may have different thermal properties compared to traditional PCB materials.
- Testing and Validation: Perform thorough testing and validation of the transparent PCB design to ensure it meets both electrical and transparency requirements. This may include optical testing to assess light transmission and uniformity.
- Manufacturing Considerations: Work closely with your PCB manufacturer to address any specific manufacturing challenges associated with transparent substrates, such as handling, processing, and assembly techniques.
By following these guidelines, you can design transparent PCBs that not only meet your functional requirements but also optimize visibility and aesthetic appeal.
What is the Transparent PCB Substrate Fabrication Process?
The fabrication process for transparent PCB substrates involves several steps tailored to the unique properties of transparent materials. Here’s an overview of the typical process:
- Material Selection: Choose a transparent substrate material suitable for your application, such as glass, acrylic, or polycarbonate. Consider factors like thermal stability, mechanical strength, and transparency.
- Preparation of Substrate Material:Prepare the transparent substrate material by cutting it to the required size and shape. Depending on the material, this may involve processes like cutting, milling, or laser cutting.
- Surface Cleaning:Thoroughly clean the substrate surface to remove any contaminants that could affect adhesion or transparency. Use appropriate cleaning solutions and techniques to ensure a pristine surface.
- Application of Transparent Conductive Layer: If transparent conductive layers are required for traces and pads, apply them to the substrate surface using techniques like sputtering, chemical vapor deposition (CVD), or screen printing. Indium tin oxide (ITO) is a common material used for transparent conductive layers.
- Photoresist Application:Apply a photoresist layer onto the substrate surface. This layer will be used to define the circuit pattern during the photolithography process.
- Exposure and Development: Use photolithography techniques to expose the photoresist layer to UV light through a photomask, which contains the desired circuit pattern. After exposure, develop the photoresist to remove the unexposed areas, leaving behind the circuit pattern.
- Etching: Etch away the exposed areas of the transparent conductive layer using chemical etchants, such as acids or alkaline solutions. This process defines the conductive traces and pads on the substrate surface.
- Surface Finishing: Apply any necessary surface finishes to the substrate to enhance transparency, protect against environmental factors, and improve solderability if required. Common surface finishes for transparent PCBs include clear coatings or finishes that provide scratch resistance.
- Component Attachment: If the transparent PCB will include components, attach them to the substrate using conventional soldering techniques or specialized methods suited to transparent materials.
- Testing and Quality Control: Perform thorough testing and quality control checks to ensure the fabricated transparent PCB substrates meet the specified requirements for transparency, electrical performance, and reliability.
- Packaging and Delivery: Package the fabricated transparent PCB substrates appropriately for protection during transportation and storage, and deliver them to the assembly facility or end users.
By following these fabrication steps, manufacturers can produce transparent PCB substrates tailored to specific applications, balancing the requirements for functionality, transparency, and reliability.
How do you manufacture a Transparent PCB Substrate?
Manufacturing a transparent PCB substrate involves specialized processes due to the unique properties of transparent materials. Here’s a step-by-step overview of the manufacturing process:
- Material Selection: Choose a transparent substrate material suitable for your application, such as glass, acrylic, or polycarbonate. Consider factors like thermal stability, mechanical strength, and transparency.
- Substrate Preparation: Cut the transparent substrate material to the required size and shape using techniques like cutting, milling, or laser cutting. Ensure that the substrate surfaces are clean and free from contaminants.
- Transparent Conductive Layer Deposition: If transparent conductive layers are needed for traces and pads, deposit them onto the substrate surface using techniques like sputtering, chemical vapor deposition (CVD), or screen printing. Indium tin oxide (ITO) is a common material used for transparent conductive layers.
- Photoresist Application: Apply a photoresist layer onto the substrate surface. This layer will serve as a mask during the patterning of the conductive layer.
- Patterning: Use photolithography techniques to define the desired circuit pattern on the photoresist-coated substrate. This involves exposing the photoresist to UV light through a photomask that contains the circuit pattern.
- Etching: Etch away the exposed areas of the transparent conductive layer using chemical etchants, such as acids or alkaline solutions. This process defines the conductive traces and pads on the substrate surface.
- Surface Finishing: Apply any necessary surface finishes to the substrate to enhance transparency, protect against environmental factors, and improve solderability if required. Common surface finishes for transparent PCBs include clear coatings or finishes that provide scratch resistance.
- Component Attachment: If the transparent PCB substrate will include components, attach them to the substrate using conventional soldering techniques or specialized methods suitable for transparent materials.
- Testing and Quality Control: Perform thorough testing and quality control checks to ensure that the fabricated transparent PCB substrate meets the specified requirements for transparency, electrical performance, and reliability.
- Packaging and Delivery:Package the fabricated transparent PCB substrates appropriately for protection during transportation and storage, and deliver them to the assembly facility or end users.
Manufacturing transparent PCB substrates requires careful attention to detail and specialized equipment to ensure that the final product meets the required specifications for transparency, functionality, and reliability.
How much should a Transparent PCB Substrate cost?
The cost of a transparent PCB substrate can vary significantly depending on several factors:
- Material: The type of transparent material used for the substrate (e.g., glass, acrylic, polycarbonate) greatly influences the cost. Glass tends to be more expensive than acrylic or polycarbonate due to its higher material and manufacturing costs.
- Size and Thickness: Larger and thicker substrates require more material and may involve additional manufacturing processes, which can increase costs.
- Complexity of Design: The complexity of the PCB design, including the number of layers, intricacy of the circuitry, and presence of special features like embedded components or lighting elements, can impact manufacturing costs.
- Manufacturing Processes:The specific manufacturing processes used, such as deposition of transparent conductive layers, photolithography, etching, and surface finishing, contribute to the overall cost.
- Quantity: Typically, ordering larger quantities of transparent PCB substrates can result in lower per-unit costs due to economies of scale.
- Quality Requirements: Higher quality standards, tighter tolerances, and additional testing or quality control measures may increase the cost but can also ensure better performance and reliability.
- Supplier and Location: The choice of supplier and their location can affect costs due to differences in labor, overhead, and transportation expenses.
As a rough estimate, transparent PCB substrates can range in cost from a few dollars to several hundred dollars per unit, depending on the factors mentioned above. For precise pricing, it’s best to contact PCB manufacturers or suppliers directly and provide detailed specifications for your specific requirements.
What is Transparent PCB Substrate base material?
Transparent PCB substrates can be made from various materials, depending on the specific requirements of the application. Some common base materials used for transparent PCB substrates include:
- Glass: Glass is a popular choice for transparent PCB substrates due to its high transparency and excellent thermal and mechanical properties. It provides good rigidity and can withstand high temperatures, making it suitable for demanding applications.
- Acrylic (PMMA): Acrylic, also known as polymethyl methacrylate (PMMA) or Plexiglas, is a transparent thermoplastic material that offers excellent optical clarity and can be easily machined or molded into complex shapes. It’s lightweight and relatively inexpensive compared to glass.
- Polycarbonate: Polycarbonate is another transparent thermoplastic material known for its high impact resistance and optical clarity. It’s often used in applications where durability and resistance to breakage are critical.
- Transparent Conductive Films: In some cases, transparent conductive films or coatings are applied to non-transparent substrates to achieve transparency while maintaining electrical conductivity. These films are typically made from materials like indium tin oxide (ITO) or graphene.
- Specialized Composite Materials: Some transparent PCB substrates may be made from specialized composite materials that combine transparent polymers with conductive additives or reinforcing fibers to achieve specific performance requirements.
The choice of base material depends on factors such as optical clarity, mechanical strength, thermal properties, cost, and manufacturing considerations. Each material has its own advantages and limitations, so it’s essential to select the most suitable material based on the requirements of the application.
Which company makes Transparent PCB Substrates?
Currently, many companies play an important role in the production of transparent PCB substrates. Some major companies include Cerambus, Nippon Electric Glass, Rogers Corporation, and SCHOTT AG. These companies utilize advanced materials processes and manufacturing technologies to produce various transparent PCB substrates, meeting the needs of different industries.
As for our company, we can also manufacture transparent PCB substrates. As a technologically advanced PCB manufacturer, we have advanced equipment and an experienced team to meet the demand for high-quality transparent PCB substrates from customers. Our production process includes the following key steps:
- Material Selection:We choose high-quality transparent substrate materials such as glass, acrylic, or polycarbonate to ensure the best optical transparency and mechanical performance.
- Design and Engineering: Our engineering team designs transparent PCB substrates according to customer specifications, optimizing layouts and stackups for the best performance.
- Processing and Manufacturing: We use advanced processing equipment and techniques to cut, drill, etch, and coat transparent substrates to create the required circuit patterns and structures.
- Application of Transparent Conductive Layer: Depending on the requirement, we apply a transparent conductive layer, such as an Indium Tin Oxide (ITO) layer, on the substrate surface for electrical connectivity.
- Surface Treatment:We apply surface treatments such as coating with a transparent protective layer or surface finish to enhance wear resistance and environmental stability.
- Quality Control and Testing:We conduct rigorous quality control procedures to inspect and test transparent PCB substrates to ensure they meet customer specifications and requirements.
Through these steps, our company is able to produce high-quality, reliable transparent PCB substrates applicable to various industries such as automotive, medical, consumer electronics, and industrial equipment. We are committed to providing customized solutions to customers and maintaining a leading position in the field of transparent PCBs.
What are the 7 qualities of good customer service?
Good customer service is characterized by several key qualities that contribute to a positive experience for customers. Here are seven qualities:
- Responsiveness: Good customer service involves being prompt and attentive to customer inquiries, concerns, and needs. Responding quickly and effectively demonstrates that the customer’s time and issues are valued.
- Empathy:Empathy involves understanding and acknowledging the customer’s feelings, concerns, and perspectives. It means putting yourself in the customer’s shoes and showing genuine compassion and understanding.
- Professionalism: Professionalism in customer service means maintaining a courteous and respectful demeanor at all times, regardless of the situation. It involves using appropriate language, tone, and behavior to interact with customers in a professional manner.
- Knowledgeability: Good customer service representatives possess a deep understanding of the products or services offered by the company. They are knowledgeable about the features, benefits, and usage of the products/services and can provide accurate information and guidance to customers.
- Problem-solving skills:Effective customer service involves the ability to resolve issues and address problems efficiently and effectively. This requires critical thinking, creativity, and resourcefulness to find solutions that meet the customer’s needs and expectations.
- Consistency: Consistency is key to good customer service. Customers expect a consistent level of service across all interactions and touchpoints with the company, whether it’s in-store, online, or over the phone. Consistency builds trust and confidence in the company’s brand.
- Follow-up and follow-through: Good customer service doesn’t end with resolving the immediate issue. It involves following up with customers to ensure that their needs have been met and their concerns have been addressed satisfactorily. Follow-through also includes taking proactive steps to prevent similar issues from arising in the future.
By embodying these qualities, businesses can deliver exceptional customer service experiences that foster loyalty, satisfaction, and positive word-of-mouth recommendations.
FAQs
What are transparent PCB substrates?
Transparent PCB substrates are printed circuit board materials that allow light to pass through, enabling visibility of components and traces embedded within. They are commonly made from transparent materials like glass, acrylic, or polycarbonate.
What are the advantages of transparent PCB substrates?
Transparent PCB substrates offer several advantages, including enhanced design aesthetics, easy identification of components, integration of lighting elements directly into the PCB, and suitability for applications where visual inspection or aesthetic appeal is important.
What applications are transparent PCB substrates used for?
Transparent PCB substrates are used in various applications, including decorative lighting, automotive displays, consumer electronics, specialty industrial equipment, and any other application where both practicality and aesthetics are important.
How are transparent PCB substrates manufactured?
The manufacturing process for transparent PCB substrates involves specialized processes tailored to the unique properties of transparent materials. It includes steps such as material selection, substrate preparation, application of transparent conductive layers, patterning, etching, surface finishing, component attachment, testing, and quality control.
What materials are used for transparent conductive layers?
Transparent conductive layers are typically made from materials like indium tin oxide (ITO), graphene, or other conductive oxides. These materials provide both transparency and electrical conductivity required for the functioning of the PCB.
Can transparent PCB substrates be customized?
Yes, transparent PCB substrates can be customized to meet specific requirements and specifications of different applications. This includes customization of size, shape, thickness, circuit layout, and other parameters based on the needs of the customer.
Are there any limitations to using transparent PCB substrates?
While transparent PCB substrates offer many benefits, they also have some limitations. For example, they may have different thermal properties compared to traditional PCB materials, and care must be taken to manage heat dissipation effectively. Additionally, the availability of materials and manufacturing processes may affect the cost and lead time of transparent PCB substrates.