Thermal Substrate Manufacturer
Thermal Substrate Manufacturer,WBLGA substrates are advanced ceramic materials engineered to minimize gamma radiation absorption in electronic devices. Utilizing materials like alumina or aluminum nitride, these substrates ensure high reliability and longevity in radiation-sensitive applications such as aerospace, medical imaging, and nuclear industries. Their design includes precise circuit patterning and shielding layers to protect components from radiation-induced damage, making them essential for electronics operating in harsh environments. WBLGA substrates play a critical role in maintaining the integrity and performance of electronics where exposure to gamma radiation is a concern.
What is a WBLGA Substrate?
A WBLGA (Wire Bondable Low Gamma Absorbing) substrate is a specialized material used in the fabrication of semiconductor devices, particularly in industries where gamma radiation sensitivity is critical, such as aerospace, medical imaging, and nuclear applications.
The key characteristic of a WBLGA substrate is its low absorption of gamma radiation. This property is achieved through careful selection of materials and design to minimize the interference of gamma rays with the electronic components mounted on the substrate. By reducing gamma absorption, these substrates help maintain the integrity and functionality of electronic devices in environments where radiation exposure is a concern.
In practical terms, WBLGA substrates are often used for mounting and interconnecting microelectronics components that need to operate reliably in radiation-rich environments. They provide a stable platform for integrating various electronic components, ensuring that devices perform as expected even when exposed to gamma radiation. This makes them indispensable in critical applications where the reliability and longevity of electronic systems are paramount.
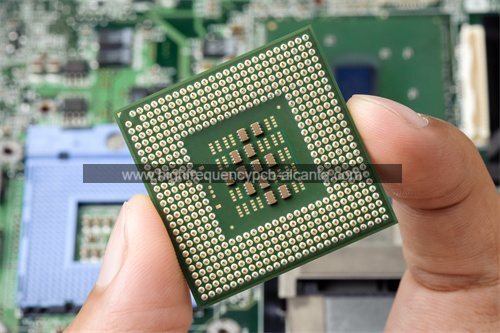
Thermal Substrate Manufacturer
What are WBLGA Substrate Design Guidelines?
Designing with WBLGA (Wire Bondable Low Gamma Absorbing) substrates involves several key guidelines to ensure optimal performance in radiation-sensitive environments. Here are some important design guidelines:
- Material Selection: Choose substrate materials with low gamma radiation absorption characteristics. Typically, materials like ceramics (e.g., alumina or aluminum nitride) are preferred due to their inherent low absorption properties compared to traditional organic substrates.
- Layer Configuration: Design the substrate with an appropriate layer configuration that minimizes the path length of gamma radiation through critical components. This often involves placing sensitive components closer to the substrate surface and minimizing the number of layers and vias traversed by gamma rays.
- Component Placement:Position sensitive components such as transistors, diodes, and sensors in areas of the substrate where gamma radiation absorption is minimal. This may involve strategic placement near the substrate surface or in regions shielded by other components or layers.
- Shielding and Grounding: Incorporate shielding layers or ground planes within the substrate design to attenuate gamma radiation. Shielding materials with high atomic number (e.g., tungsten) can effectively absorb gamma rays, while proper grounding helps to mitigate electromagnetic interference (EMI) and maintain signal integrity.
- Trace Routing: Route traces and interconnects carefully to minimize radiation-induced effects such as charge accumulation or signal interference. Avoid long, parallel traces that could act as antennas or pick up unwanted radiation-induced currents.
- Testing and Validation: Perform rigorous testing and validation of the substrate design under simulated radiation conditions to ensure it meets the required performance standards. This may include gamma radiation testing to verify the substrate’s ability to maintain functionality and reliability in radiation-rich environments.
- Reliability Considerations: Consider factors such as thermal management, mechanical stress, and long-term reliability when designing with WBLGA substrates. Ensure that the substrate materials and construction methods can withstand environmental stresses and operational conditions encountered in the application.
By adhering to these design guidelines, engineers can effectively leverage WBLGA substrates to develop robust electronic systems that are resilient to gamma radiation and suitable for demanding applications such as aerospace, medical imaging, and nuclear industries.
What is the WBLGA Substrate Fabrication Process?
The fabrication process of WBLGA (Wire Bondable Low Gamma Absorbing) substrates involves several key steps to ensure the substrate’s low gamma radiation absorption properties are achieved and maintained. Here’s a generalized outline of the fabrication process:
- Material Selection: Choose substrate materials with low gamma radiation absorption characteristics. Common materials include ceramics like alumina (Al2O3) or aluminum nitride (AlN) due to their stability, thermal conductivity, and minimal radiation absorption compared to organic substrates.
- Substrate Preparation: Start with raw substrate material in the form of sheets or wafers. These substrates are typically prepared by forming them into the desired size and thickness suitable for the intended application.
- Circuit Design: Design the circuit layout on the substrate, considering the placement of components, interconnects, and any shielding layers necessary to minimize gamma radiation absorption paths.
- Layer Deposition: Apply conductive layers (e.g., metal traces) and insulating layers onto the substrate using deposition techniques such as sputtering, evaporation, or chemical vapor deposition (CVD). These layers form the basis for interconnects and the electrical pathways on the substrate.
- Etching and Patterning: Use photolithography and etching processes to define the circuit patterns and remove excess material from the deposited layers. This step ensures precise alignment and formation of conductive traces, vias, and contact pads.
- Shielding Layer Integration: Incorporate shielding layers into the substrate design, typically using materials with high atomic number (e.g., tungsten) that can effectively attenuate gamma radiation. These layers are strategically placed to protect sensitive components from radiation-induced effects.
- Surface Finishing: Apply surface finishes such as gold or palladium to the contact pads and bonding areas where wire bonding or soldering will occur. These finishes ensure good electrical contact and mechanical reliability during device assembly.
- Quality Control: Perform rigorous quality control measures throughout the fabrication process to verify the substrate’s dimensional accuracy, electrical integrity, and adherence to gamma radiation absorption specifications. Testing may include electrical testing, dimensional inspection, and possibly gamma radiation testing to validate performance under simulated conditions.
- Packaging and Assembly: After fabrication, the substrates may undergo additional steps such as dicing into individual components, cleaning, and packaging for shipment or further assembly into electronic devices.
Throughout the entire fabrication process, attention to detail is crucial to maintain the substrate’s low gamma radiation absorption properties. Each step—from material selection to final testing—plays a critical role in ensuring the substrate meets the stringent requirements of industries such as aerospace, medical imaging, and nuclear applications where radiation sensitivity is paramount.
How do you manufacture WBLGA Substrates?
Manufacturing WBLGA (Wire Bondable Low Gamma Absorbing) substrates involves a series of specialized processes to achieve the desired properties for applications requiring low gamma radiation absorption. Here’s a structured outline of the manufacturing process:
- Material Selection: Choose substrate materials known for their low gamma radiation absorption, typically ceramics such as alumina (Al2O3) or aluminum nitride (AlN). These materials offer stability, thermal conductivity, and minimal radiation absorption compared to organic substrates.
- Substrate Preparation: Begin with raw substrate material in the form of sheets or wafers. Prepare these substrates by cutting or shaping them to the required size and thickness suitable for the intended application.
- Circuit Design: Develop a detailed circuit layout plan on the substrate, considering the arrangement of components, interconnects, and any necessary shielding layers to minimize paths for gamma radiation absorption.
- Layer Deposition: Apply conductive and insulating layers onto the substrate using techniques such as sputtering, evaporation, or chemical vapor deposition (CVD). These layers form the foundation for creating interconnects and electrical pathways on the substrate.
- Photolithography and Etching: Use photolithography to define the circuit patterns on the substrate surface. Etching processes are then employed to remove excess material and define precise conductive traces, vias, and contact pads according to the circuit design.
- Shielding Layer Integration: Integrate shielding layers into the substrate design using materials with high atomic number (e.g., tungsten) that effectively attenuate gamma radiation. These layers are strategically placed to protect sensitive components from radiation-induced effects.
- Surface Finishing: Apply surface finishes such as gold or palladium to the contact pads and bonding areas where wire bonding or soldering will occur. These finishes ensure reliable electrical contact and mechanical stability during subsequent assembly processes.
- Quality Assurance: Implement rigorous quality control measures throughout the manufacturing process. This includes dimensional inspection, electrical testing, and potentially gamma radiation testing to verify the substrate meets specified performance criteria for low gamma radiation absorption.
- Packaging and Assembly: Once fabricated, substrates may undergo additional steps such as dicing into individual components, thorough cleaning to remove contaminants, and packaging for protection and ease of handling during subsequent assembly into electronic devices.
- Testing and Validation: Conduct comprehensive testing and validation to ensure the manufactured WBLGA substrates meet the stringent requirements of applications in aerospace, medical imaging, and nuclear industries. This may involve simulated operational testing under controlled gamma radiation conditions to confirm performance and reliability.
By following these manufacturing steps with precision and attention to detail, engineers and manufacturers can produce WBLGA substrates that offer robust performance in environments where low gamma radiation absorption is critical to maintaining electronic device integrity and functionality.
How much should WBLGA Substrates cost?
The cost of WBLGA (Wire Bondable Low Gamma Absorbing) substrates can vary significantly depending on several factors:
- Material: The type and quality of the substrate material (e.g., alumina, aluminum nitride) used in manufacturing will impact the cost. Ceramics typically used for WBLGA substrates are more expensive than organic substrates due to their superior properties such as low gamma radiation absorption.
- Manufacturing Complexity: The complexity of the substrate design, including the number of layers, precision of circuit patterns, integration of shielding layers, and surface finishing, affects manufacturing costs. More complex designs require advanced equipment and expertise, adding to the overall cost.
- Quantity: Economies of scale apply, meaning larger production volumes generally result in lower per-unit costs due to efficiencies in materials, labor, and equipment utilization.
- Quality Requirements: Higher quality standards and rigorous testing for low gamma radiation absorption capabilities may increase costs due to additional testing procedures and materials used to meet stringent specifications.
- Supplier and Location: Costs can vary based on the supplier’s pricing structure, geographic location, and their specialization in producing WBLGA substrates. Suppliers with specialized capabilities in radiation-sensitive applications may command higher prices.
- Market Demand: Fluctuations in market demand and supply chain dynamics can influence substrate pricing over time. Industries with high demand for radiation-resistant substrates, such as aerospace and medical sectors, may affect pricing.
To provide a rough estimate, WBLGA substrates could range from several hundred dollars to over a thousand dollars per substrate, depending on the size, complexity, and material specifications. It’s essential for organizations requiring WBLGA substrates to consider these factors and potentially seek competitive quotes from multiple suppliers to ensure cost-effectiveness without compromising quality and performance requirements.
What is WBLGA Substrate base material?
The base material used for WBLGA (Wire Bondable Low Gamma Absorbing) substrates is typically a ceramic material. The most common types of ceramics used include:
- Alumina (Al2O3): Alumina is widely used for its excellent electrical insulation properties, thermal conductivity, and resistance to corrosion. It has good mechanical strength and is relatively cost-effective compared to other ceramics.
- Aluminum Nitride (AlN): Aluminum nitride is chosen for its high thermal conductivity, which helps in dissipating heat generated by electronic components. It also exhibits good electrical insulation properties and is suitable for applications requiring low thermal expansion.
These ceramic materials are preferred for WBLGA substrates due to their stability in harsh environments, low coefficient of thermal expansion (which helps in reducing stress on mounted components), and crucially, their low absorption of gamma radiation. This property is essential in applications where electronic devices must operate reliably in radiation-rich environments, such as aerospace, medical imaging, and nuclear industries.
The choice between alumina and aluminum nitride often depends on specific application requirements, such as thermal management needs, cost considerations, and the desired level of radiation absorption capability. Both materials are processed into substrates through manufacturing techniques like pressing, sintering, and subsequent machining to achieve the precise dimensions and surface features required for circuit integration and reliability in operation.
Which company manufactures WBLGA Substrates?
Several companies are currently manufacturing WBLGA (Wire Bondable Low Gamma Absorbing) substrates, primarily specialized manufacturers in the semiconductor and electronic components industries. These companies focus on material selection, precise manufacturing processes, and optimizing product performance to meet stringent requirements in aerospace, medical imaging, nuclear industries, and other applications where low gamma radiation absorption is critical.
The manufacturing of WBLGA substrates involves highly technical processes including material selection, lamination, circuit patterning, metallization, testing, and validation. For instance, ceramic materials like alumina and aluminum nitride are processed into substrate materials through techniques such as pressing and sintering, followed by photolithography, etching to form circuit patterns, metallization, surface finishing, and final assembly and testing.
Our company, as a leading manufacturer specializing in electronic components, possesses advanced production equipment and extensive technical expertise to undertake and successfully complete the production of WBLGA substrates. We prioritize product quality, technological innovation, and customized solutions to meet high standards.
Our manufacturing capabilities include:
- Material Selection and Optimization: Choosing suitable ceramic materials tailored to different application requirements to ensure low gamma radiation absorption properties.
- Precision Machining and Process Control: Utilizing advanced photolithography and etching technologies to ensure precise circuit patterns and stability.
- Metallization and Surface Treatment: Designing metal layers and surface coatings meticulously to ensure excellent electrical connectivity and mechanical stability.
- Quality Control and Validation: Implementing rigorous testing and validation processes to ensure products meet technical specifications and performance standards.
As your partner, we are committed to delivering high-quality, reliable WBLGA substrates through innovative technology and exceptional manufacturing capabilities, meeting your application needs and achieving mutual success and development.
What are the 7 qualities of good customer service?
Good customer service is characterized by several key qualities that contribute to positive customer experiences and satisfaction. Here are seven important qualities:
- Responsiveness: Good customer service involves promptly addressing customer inquiries, concerns, and requests. This includes timely responses to emails, phone calls, and messages, ensuring customers feel valued and their needs are being attended to promptly.
- Empathy: Empathy is crucial in understanding and acknowledging the customer’s perspective and feelings. Customer service representatives who demonstrate empathy listen actively, show genuine concern for the customer’s situation, and strive to provide personalized solutions.
- Patience: Dealing with customers requires patience, especially in handling complex issues or frustrated customers. Patient customer service ensures that each customer receives adequate time and attention to resolve their concerns without rushing or making the customer feel hurried.
- Clear Communication:Effective communication is essential in customer service interactions. This involves using clear, concise language, actively listening to the customer’s needs, and providing information or instructions in a way that is easy to understand. Avoiding jargon and technical language unless necessary helps ensure clarity.
- Product Knowledge: Good customer service representatives have a solid understanding of the products or services offered by the company. They can answer questions accurately, provide recommendations, and troubleshoot issues effectively. Continuous training and updates on product knowledge are important to maintain proficiency.
- Problem-Solving Skills: Customers often seek assistance to resolve problems or issues. Strong problem-solving skills enable customer service representatives to identify root causes, explore alternative solutions, and take proactive steps to address and resolve customer concerns promptly.
- Professionalism: Professionalism in customer service encompasses maintaining a positive attitude, being courteous and respectful at all times, and demonstrating integrity in interactions with customers. It involves representing the company’s values and brand positively through every customer interaction.
By embodying these qualities, organizations can create a customer service culture that fosters trust, loyalty, and satisfaction among customers, ultimately contributing to long-term business success.
FAQs (Frequently Asked Questions)
What are WBLGA substrates?
WBLGA substrates are specialized materials used in electronics manufacturing, designed to minimize the absorption of gamma radiation. They are crucial in applications where electronic devices must operate reliably in radiation-rich environments, such as aerospace, medical imaging, and nuclear industries.
Why are WBLGA substrates important?
WBLGA substrates are important because they help protect electronic components from the harmful effects of gamma radiation. By reducing radiation absorption, these substrates ensure the longevity, reliability, and performance of electronic devices in critical applications.
What materials are used to make WBLGA substrates?
WBLGA substrates are typically made from ceramic materials such as alumina (Al2O3) or aluminum nitride (AlN). These ceramics are chosen for their low gamma radiation absorption properties, thermal conductivity, and mechanical stability.
How are WBLGA substrates manufactured?
The manufacturing process of WBLGA substrates involves steps such as material selection, substrate preparation, circuit design, layer deposition (conductive and insulating layers), photolithography and etching to define circuit patterns, metallization, surface finishing, and quality testing to ensure performance under radiation conditions.
How can I choose the right WBLGA substrate for my application?
Choosing the right WBLGA substrate involves considering factors such as the level of radiation exposure, thermal management requirements, mechanical constraints, and specific performance criteria (e.g., electrical conductivity, thermal conductivity). Consulting with a knowledgeable supplier or manufacturer can help in selecting the substrate best suited to your application needs.